FAQ List
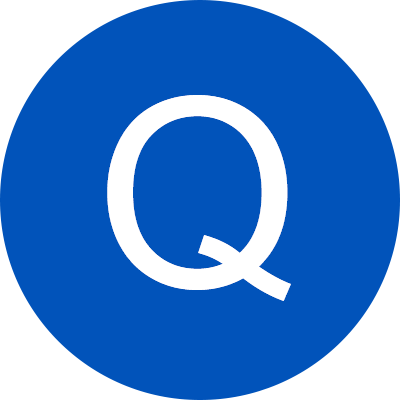
A brief discussion on the eddy current inspection method of steel wire
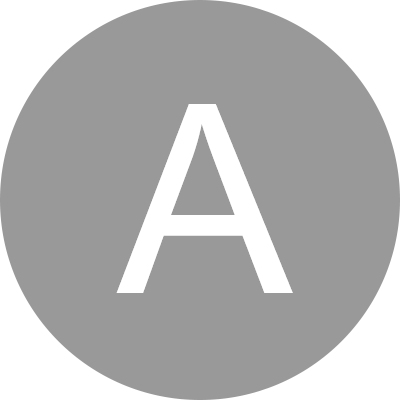
At present, there are many methods for steel wire detection, among which there are representative methods: ultrasonic testing method, eddy current testing method, magnetic leakage testing method. Eddy current testing is a technology which has developed rapidly in recent years. The schematic diagram of the method used for steel wire inspection is shown in figure 4-1.
Steel wire is a strong magnetic material, and due to cold drawing and other reasons, the surface permeability has significant differences in different places, in the detection, the permeability is not uniform is the main reason for generating mixed signals. In this case, dc magnetic saturation device can be used to test the specimen in the state of saturation magnetization. Due to saturation magnetization, the unevenness of permeability is reduced, thus the signal can be always mixed. Due to the fact that the eddy current method does not require direct contact with the specimen and does not fill the lotus root mixture between the coil and the specimen, it is easy to realize online detection and has high detection speed and efficiency, so it is widely used in the inspection of steel wire defects. Due to skin effect, eddy current method is mainly used to detect surface cracks and near surface cracks.
Due to the existence of high frequency excitation signals, eddy current detection method is easy to cause mutual interference of signals, which brings certain difficulties to the processing of detection signals. In addition, the change of relative velocity between the detection coil and the tested part has great influence on the detection accuracy. Since it is difficult to manufacture some coils, most of the detection sensors are through coils. For logging wire, the installation of closed detection coils on site is very inconvenient or almost impossible. Because the working environment of logging steel wire is very bad, the form of defects is various, not only there are internal and external fatigue cracks caused by long-term stress, but also there are defects such as porosity and rust. The magnetic leakage detection method has the characteristics of high detection sensitivity, simple structure, convenient signal processing and strong anti-interference ability.
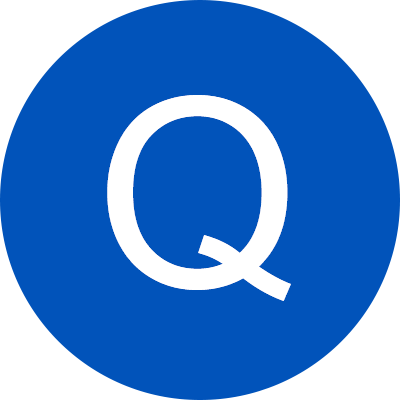
Three major factors should be considered when selecting steel wire diameter
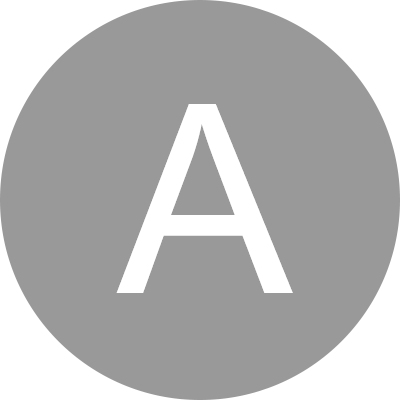
As we all know, even the steel wire of the same kind of steel, because the steelmaking process, wire drawing process and equipment are not the same in each steel plant, so the quality of steel wire is not the same. And because of the mechanical properties of the wire itself, the flattening process and equipment, the wire in the flattening process of the width and elongation have different effects. Therefore, the following factors should be considered when selecting the diameter of the wire.
The influence of tensile strength or hardness of steel wire
Steel wire tensile strength, high hardness, in the rolling flat process, steel wire unit volume longitudinal movement resistance increases, elongation decreases. And the unit volume of steel wire will be smaller lateral movement, wide expansion. On the contrary, steel wire tends to lengthwise elongation, its width decreases. This is also the production of high steel wire hardness is easy to wide, hardness is small, easy to elongation and not wide reason. If the tensile strength deviation of steel wire is large and the hardness uniformity of steel wire is poor, then the width difference of rolling billet will seriously affect the quality of billet.
Second, the effect of steel wire surface roughness
In the rolling process, if the surface of steel wire is rough, the relative friction coefficient between steel wire and roller increases, the friction resistance increases, steel wire elongation decreases, width increases. Production with the weight of the skin of the material is easy to be wide, because of its rough surface. On the contrary, the surface of the steel wire is smooth, because the friction resistance between the steel wire and the roller is small, relatively easy to extend, the width is small. Domestic steel wire in order to prevent rust, the surface coated with butter, such as butter removal is not clean, easy to slip when rolling flat, but also affect its wide.
The influence of chemical composition and microstructure of steel wire
The higher the carbon content of steel wire, the less its plasticity, steel wire section compression and elongation, steel wire in the rolling deformation difficulties, small width. For alloy steel wire, because the alloy element dissolved in the solid solution can improve the hardening rate of steel wire in cold work, its deformation resistance, rolling width is small, and easy to brittle.
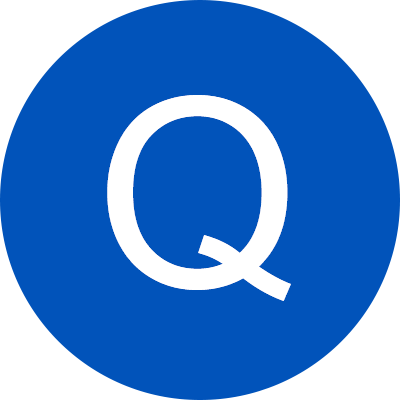
Eight working procedures of prestressing steel wire marshalling
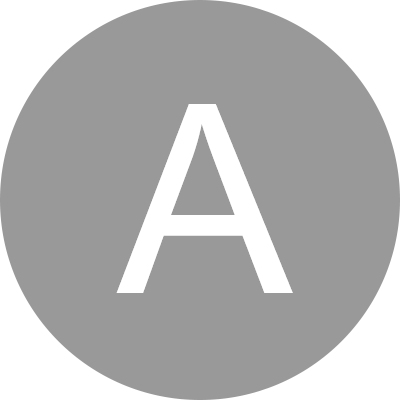
Prestressing steel wire marshalling equipment mainly includes steel wire reversing machine, steel wire tray, steel wire pressure machine, corrugated fixture, fixture assembly table, fixture press, steel wire drawing machine and pendulum steel wire friction saw. Wire marshalling mainly includes the following processes:
One, steel wire upside down. The qualified steel wire will be transported from the warehouse to the workshop, and the steel wire will be inverted on the steel wire disc by the steel wire reversing machine.
Second, the installation of steel wire disc. Steel wire: after mounting the steel wire tray, mount the steel wire tray on the steel wire rack. Each assembly line has two steel wire trays and 48 steel wire trays can be installed.
Three, steel wire pressure wave. In order to improve the grip between steel wire and concrete, the steel wire needs to be treated by compression wave. Steel wire through tooth shape after the wave roller to form a waveform steel wire, the wave distance is generally 40 mm, wave height is 1.5-2.0 mm.
Four, steel wire positioning. After the steel wire is pressed through the steel wire positioner at the front end of the fixture assembly table (horizontal positioning and vertical positioning), the steel wire is arranged in place and enters the fixture assembly table.
Installation of corrugated fixture. Corrugated clamps hold groups of steel wires firmly for tensioning. At present, there are two kinds of corrugated clamps, one is two-wave clamps, the other is three-wave clamps. When installing the corrugated clamp, place the corrugated clamp between each layer of steel wire on the fixture assembly table, and then press with the corrugated clamp press, and tighten the nut. In this way the whole group of steel wire is compressed, steel wire position can also meet the design requirements.
Stretch steel wire group. Pull the installed corrugated fixture from one end to the other end with the wire drawing machine. Because each steel wire is subjected to certain force when the steel wire passes through the wave press, the length of each steel wire in the steel wire group is basically the same. The corrugated clamp at the end of the wire group is pulled to a certain position on the drawing machine and automatically stops the stretching through the control of the travel switch. Then two sets of corrugated clamps are continuously installed at the other end of the wire set.
Seven, cut the wire. When the two ends of the steel wire group are installed with a corrugated clamp, the steel wire is cut with a pendulum friction saw. This completes the marshalling of a wire set.
Eight, steel wire into the mold. The wire marshalling process is continuous. The clamp hook of the drawing machine can be made into a steel wire group once and again with a vice. After finishing the steel wire marshalling, transfer the steel wire together with the corrugated clamps at both ends into the sleeper model.
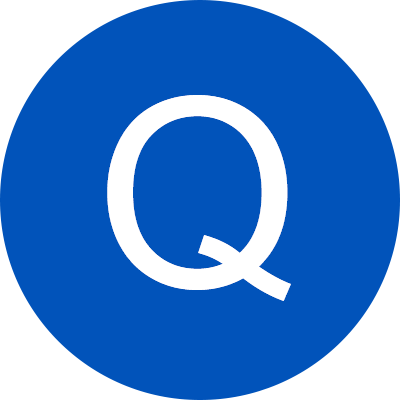
A brief discussion on the eddy current inspection method of steel wire
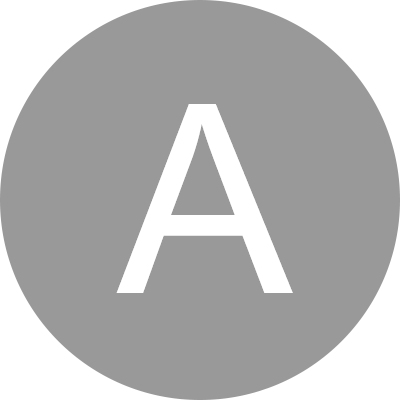
At present, there are many methods for steel wire detection, among which there are representative methods: ultrasonic testing method, eddy current testing method, magnetic leakage testing method. Eddy current testing is a technology which has developed rapidly in recent years. The schematic diagram of the method used for steel wire inspection is shown in figure 4-1.
Steel wire is a strong magnetic material, and due to cold drawing and other reasons, the surface permeability has significant differences in different places, in the detection, the permeability is not uniform is the main reason for generating mixed signals. In this case, dc magnetic saturation device can be used to test the specimen in the state of saturation magnetization. Due to saturation magnetization, the unevenness of permeability is reduced, thus the signal can be always mixed. Due to the fact that the eddy current method does not require direct contact with the specimen and does not fill the lotus root mixture between the coil and the specimen, it is easy to realize online detection and has high detection speed and efficiency, so it is widely used in the inspection of steel wire defects. Due to skin effect, eddy current method is mainly used to detect surface cracks and near surface cracks.
Due to the existence of high frequency excitation signals, eddy current detection method is easy to cause mutual interference of signals, which brings certain difficulties to the processing of detection signals. In addition, the change of relative velocity between the detection coil and the tested part has great influence on the detection accuracy. Since it is difficult to manufacture some coils, most of the detection sensors are through coils. For logging wire, the installation of closed detection coils on site is very inconvenient or almost impossible. Because the working environment of logging steel wire is very bad, the form of defects is various, not only there are internal and external fatigue cracks caused by long-term stress, but also there are defects such as porosity and rust. The magnetic leakage detection method has the characteristics of high detection sensitivity, simple structure, convenient signal processing and strong anti-interference ability.
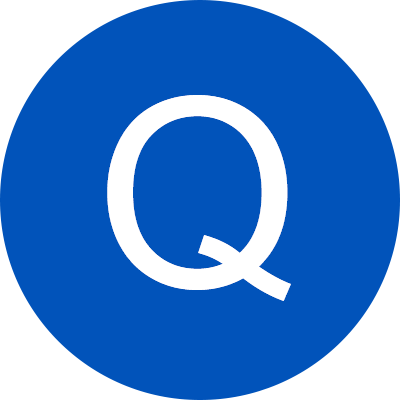
Three major factors should be considered when selecting steel wire diameter
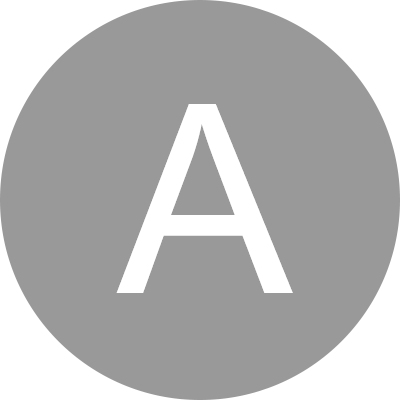
As we all know, even the steel wire of the same kind of steel, because the steelmaking process, wire drawing process and equipment are not the same in each steel plant, so the quality of steel wire is not the same. And because of the mechanical properties of the wire itself, the flattening process and equipment, the wire in the flattening process of the width and elongation have different effects. Therefore, the following factors should be considered when selecting the diameter of the wire.
The influence of tensile strength or hardness of steel wire
Steel wire tensile strength, high hardness, in the rolling flat process, steel wire unit volume longitudinal movement resistance increases, elongation decreases. And the unit volume of steel wire will be smaller lateral movement, wide expansion. On the contrary, steel wire tends to lengthwise elongation, its width decreases. This is also the production of high steel wire hardness is easy to wide, hardness is small, easy to elongation and not wide reason. If the tensile strength deviation of steel wire is large and the hardness uniformity of steel wire is poor, then the width difference of rolling billet will seriously affect the quality of billet.
Second, the effect of steel wire surface roughness
In the rolling process, if the surface of steel wire is rough, the relative friction coefficient between steel wire and roller increases, the friction resistance increases, steel wire elongation decreases, width increases. Production with the weight of the skin of the material is easy to be wide, because of its rough surface. On the contrary, the surface of the steel wire is smooth, because the friction resistance between the steel wire and the roller is small, relatively easy to extend, the width is small. Domestic steel wire in order to prevent rust, the surface coated with butter, such as butter removal is not clean, easy to slip when rolling flat, but also affect its wide.
The influence of chemical composition and microstructure of steel wire
The higher the carbon content of steel wire, the less its plasticity, steel wire section compression and elongation, steel wire in the rolling deformation difficulties, small width. For alloy steel wire, because the alloy element dissolved in the solid solution can improve the hardening rate of steel wire in cold work, its deformation resistance, rolling width is small, and easy to brittle.
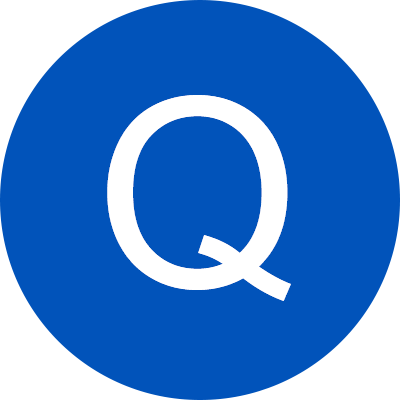
Eight working procedures of prestressing steel wire marshalling
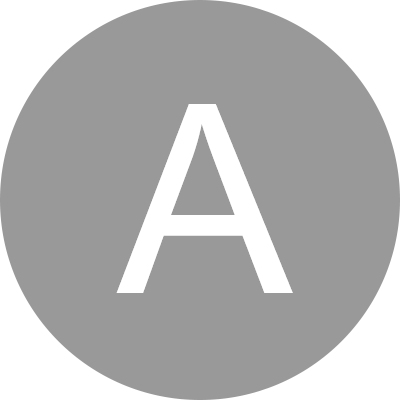
Prestressing steel wire marshalling equipment mainly includes steel wire reversing machine, steel wire tray, steel wire pressure machine, corrugated fixture, fixture assembly table, fixture press, steel wire drawing machine and pendulum steel wire friction saw. Wire marshalling mainly includes the following processes:
One, steel wire upside down. The qualified steel wire will be transported from the warehouse to the workshop, and the steel wire will be inverted on the steel wire disc by the steel wire reversing machine.
Second, the installation of steel wire disc. Steel wire: after mounting the steel wire tray, mount the steel wire tray on the steel wire rack. Each assembly line has two steel wire trays and 48 steel wire trays can be installed.
Three, steel wire pressure wave. In order to improve the grip between steel wire and concrete, the steel wire needs to be treated by compression wave. Steel wire through tooth shape after the wave roller to form a waveform steel wire, the wave distance is generally 40 mm, wave height is 1.5-2.0 mm.
Four, steel wire positioning. After the steel wire is pressed through the steel wire positioner at the front end of the fixture assembly table (horizontal positioning and vertical positioning), the steel wire is arranged in place and enters the fixture assembly table.
Installation of corrugated fixture. Corrugated clamps hold groups of steel wires firmly for tensioning. At present, there are two kinds of corrugated clamps, one is two-wave clamps, the other is three-wave clamps. When installing the corrugated clamp, place the corrugated clamp between each layer of steel wire on the fixture assembly table, and then press with the corrugated clamp press, and tighten the nut. In this way the whole group of steel wire is compressed, steel wire position can also meet the design requirements.
Stretch steel wire group. Pull the installed corrugated fixture from one end to the other end with the wire drawing machine. Because each steel wire is subjected to certain force when the steel wire passes through the wave press, the length of each steel wire in the steel wire group is basically the same. The corrugated clamp at the end of the wire group is pulled to a certain position on the drawing machine and automatically stops the stretching through the control of the travel switch. Then two sets of corrugated clamps are continuously installed at the other end of the wire set.
Seven, cut the wire. When the two ends of the steel wire group are installed with a corrugated clamp, the steel wire is cut with a pendulum friction saw. This completes the marshalling of a wire set.
Eight, steel wire into the mold. The wire marshalling process is continuous. The clamp hook of the drawing machine can be made into a steel wire group once and again with a vice. After finishing the steel wire marshalling, transfer the steel wire together with the corrugated clamps at both ends into the sleeper model.
Tel: 0086-13806168890
Fax: 0086-510-86103090
E-mail: shi_junping@fastennewcentury.com
Address: #608, No.218 Changjiang Road, Mingdu Mansion, Jiangyin, Jiangsu, China